Integration Examples¶
In this section, a series of examples will be presented so that the user knows how to configure certain customizations in the BCS PDI Builder. In addition, some examples of integration between BCS and external devices are explained.
Communication with PC¶
Since BCS can be connected to a computer via a USB or serial interface, the configuration for both connections is already set by default in BCS PDI Builder.
However, users should check that this configuration has not been modified to ensure a correct communication via both ways in case one of them is lost. To verify this:
Go to Input/Output menu \(\rightarrow\) I/O Setup section. Each USB, RS232 and RS485 Producers must be bidirectionally connected to a Commgr port:
Important
Users should also check that Commgr ports to which USB and serial ports are connected are not routed. For more information on Routing, see Ports section of this manual.
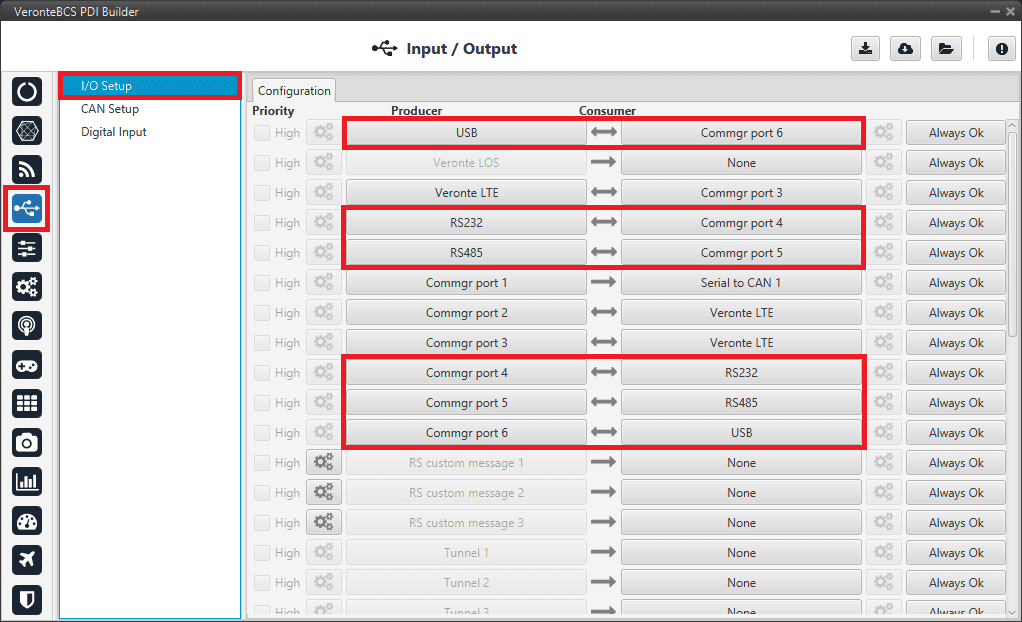
USB/RS232/RS485 \(\leftrightarrow\) Commgr port¶
CAN communication¶
This section describes how to correctly receive and transmit CAN messages:
CAN messages reception

CAN messages reception diagram¶
Go to Input/Output menu \(\rightarrow\) CAN Setup section \(\rightarrow\) Mailboxes tab.
Configure the mailbox to receive a message with the appropiate ID (in this example ID 28 has been configured):
Mailbox configuration¶
Go to Input/Output menu \(\rightarrow\) CAN Setup section \(\rightarrow\) Configuration tab.
Connect an Input filter with the right CAN ID to a Custom message consumer:
Input filter¶
Input filter configuration¶
Go to Input/Output menu \(\rightarrow\) CAN Setup section \(\rightarrow\) Custom message 1 tab (as Custom Message 1 has been selected as consumer).
Configure the message reading as desired in the RX tab by setting the correct CAN ID.
The different options and parameters to be configured are explained in the RX messages -> Custom messages section of this manual.
Custom Message configuration¶
CAN messages transmission
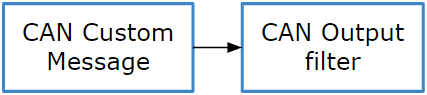
CAN messages transmission diagram¶
Go to Input/Output menu \(\rightarrow\) CAN Setup section \(\rightarrow\) Custom message 1 tab.
Select the fields to send in the TX or TX Ini section, as it is a Producer. More information on the configuration of CAN messages can be found in the TX messages -> Custom messages section of this manual.
For example, a CAN messsage set to ID 12:
Custom Message configuration¶
Go to Input/Output menu \(\rightarrow\) CAN Setup section \(\rightarrow\) Configuration tab.
Connect CAN custom message 1 producer (as the message has been configured in the Custom Message 1 tab) to an Output Filter as follows:
Output filter¶
Warning
Remember that it is necessary to have at least 1 free mailbox for TX messages.
Data transmission between BCS and 1x Autopilot¶
To stablish proper communication between ground and air units, the telemetry and sniffer menus must be configured, respectively.
A simple example of use between a ground unit (BCS) and an air unit (1x) is shown below:
In the BCS:
Go to Telemetry menu \(\rightarrow\) Telemetry section \(\rightarrow\) Data link to VApp tab (see Telemetry section, for more information about this).
Add the variables: Absolute: UAV position, Yaw, Pitch and Roll.
Set a Frequency, it is recommended to set it to 10 Hz.
On Address, point to the 1x air unit (it is needed to have both units connected through the radio in order to be able to see them on the menu).
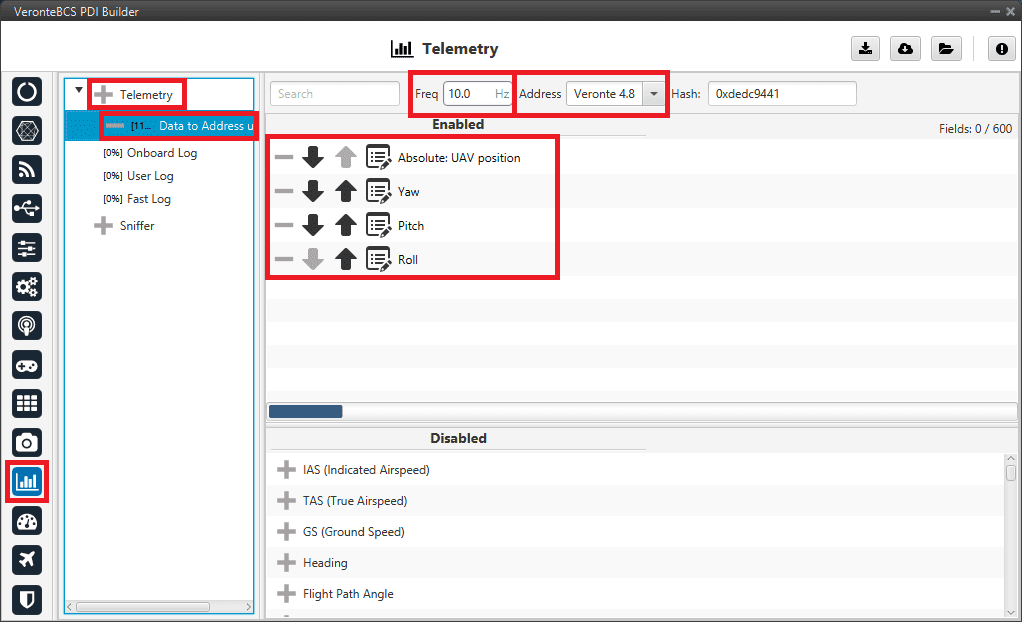
BCS ground unit - Telemetry¶
For the 1x air unit use 1x PDI Builder:
Go to Telemetry menu \(\rightarrow\) Sniffer section (for more information about this, see Sniffer section).
Add a new Sniffer.
Configure the same variables (keeping the same order) than in the ground unit.
On Address, point to the BCS ground unit.
In the gear next to it, configure the 4 incoming variables as System Variables: assign UAV Position to Moving Object and the 3 variables from attitude to 3 different User Variables (keeping the same order as well).
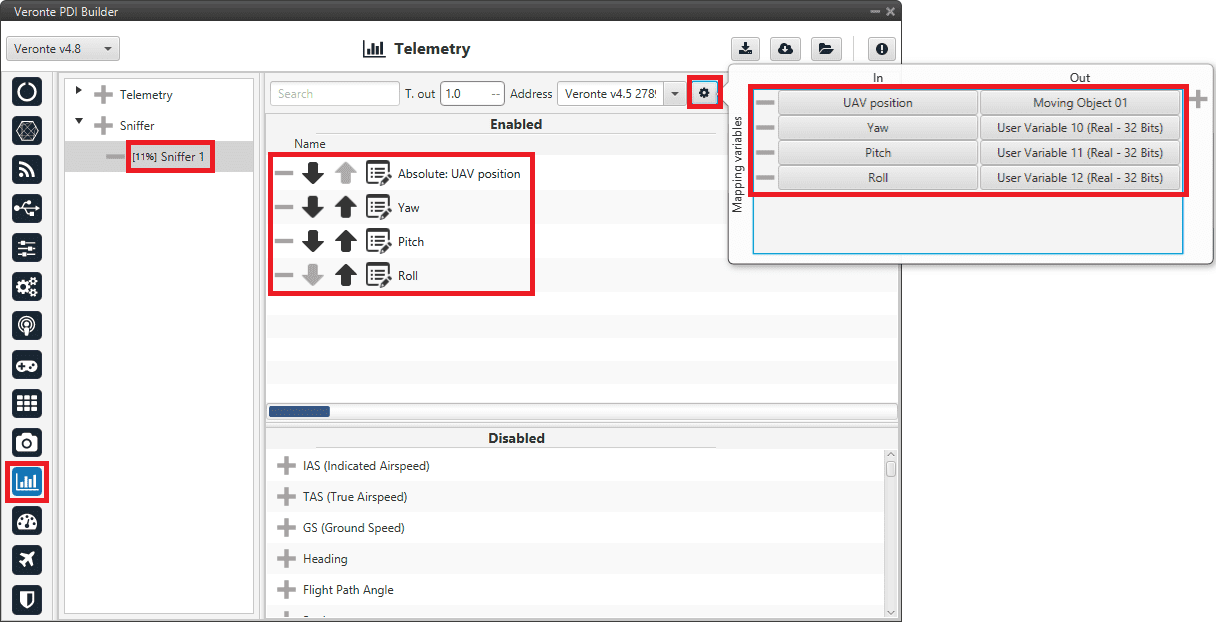
1x air unit - Sniffer¶
External devices¶
The step-by-step instructions for the following external devices will be explained in detail in the following sections: